CNC Turn-Mill Lathe Machining of an Electrical Pylon Sleeve
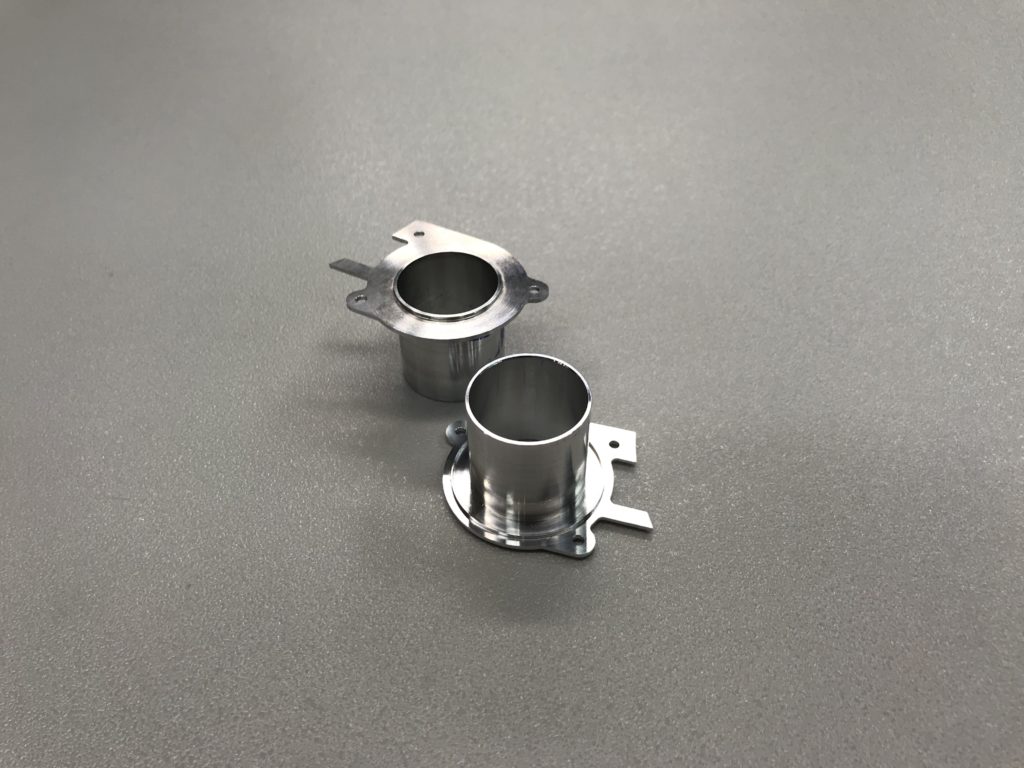
MF Engineering provides CNC turn-mill lathe machining services for industrial manufacturers in high-tech industries. We produce custom machined components for electronics, defense, and biomedical manufacturers that meet or exceed ISO 9001:2015 standards. We use a Keyence Dimension Measurement system to perform in-process dimensional inspections.
With our capabilities, we can produce between 1500-2500 components per year with conveniently scheduled releases that are delivered right to your northwest United States location.
Our special features and processes include:
- The use of 7075-T7351 aluminum
- Precision turning and boring
- Contour milling
- Off-center drilling
- Face grooving
During our combined turning and milling processes, we can maintain:
- Diametric tolerances of +/- 0.0005”
- Surface finish less than 16 micro inches
- Runout less than 0.001”
- Perpendicularity less than 0.001”
MF Engineering partners with manufacturers in the defense electronics industry to provide CNC turn-mill lathe machining of electrical pylon sleeves.
Recent Success with CNC Turn-Mill Lathe Machining for Electrical Pylon Sleeves
A recent machining project completed by MF Engineering showcases our ability to provide custom-machined components to stringent requirements. During this project, our engineering team was challenged to hold space-grade tolerances while applying various surface finishes.
Our team’s ability to perform complex machining operations and use cutting-edge Keyence IM technology to inspect geometrically complex components were instrumental in our successful completion of this project. In addition, our team members worked closely with the client to help us refine project parameters, ensuring that the client received exactly what they needed.
Our customer selected MF Engineering based on our competitive pricing, convenient location, and proven record of producing high-precision products. This project required a period of trial-and-error while our team worked to dial in our machine operations to meet customer expectations. Expedient inspections were also a challenge, as the geometry of the parts were difficult to accommodate with existing methods. However, our engineers were able to successfully overcome these challenges and produce components that satisfied our customer’s requirements.
Multiple team members contributed to our efforts to provide superior services and products. Our lead manufacturing engineer, turn-mill machinist, production manager, and quality manager all played important roles at various stages of this project. In addition, MF Engineering’s Owner/President took an active role in ensuring this order was completed as directed.
Project Results That Bring Satisfaction
Despite the unique challenges of this project, MF Engineering completed and delivered the components according to schedule. Each part was inspected and certified to meet the client’s initial specifications. Our customer was pleased with our ability to provide high-quality components that fit their demands.
Adjustments were needed throughout the project to refine the processes and design. Each time the initial plan changed, our team members were able to make the shift and continue fulfilling the customer’s requirements. In the end, the client expressed appreciation for our flexibility and professionalism. Our dedicated work earned their repeat business. Since 2015, this client has returned to us every year for their CNC turn-mill lathe machining projects.
Working with MF Engineering
Partner with MF Engineering to ensure the success of your next CNC turn-mill lathe machining project. Please contact us or request a quote for more information about our capabilities and services.